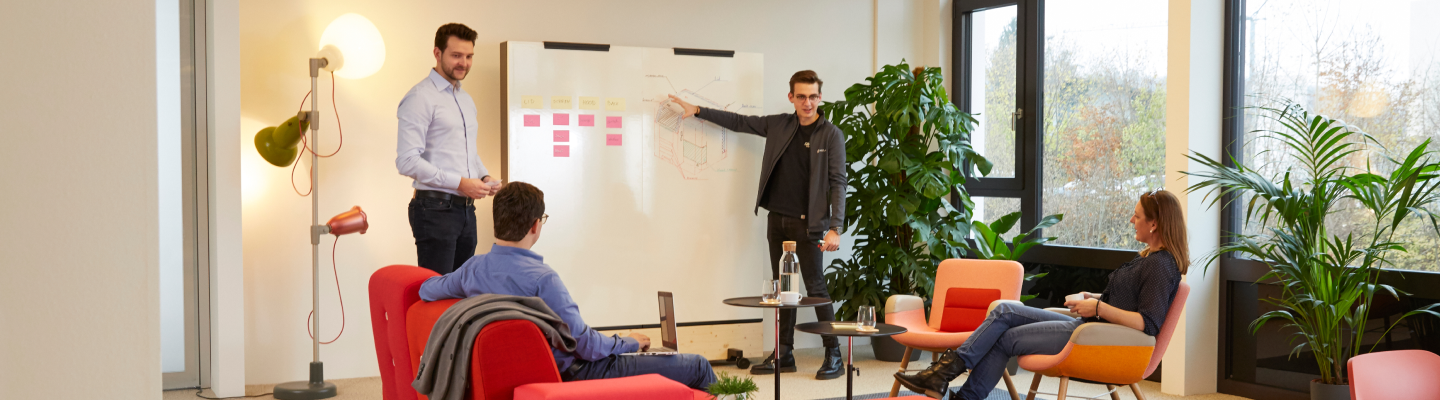
Our approach for successful projects
We understand the complex needs of the life sciences and diagnostics industry and are dedicated to delivering custom-tailored solutions to meet your specific requirements.
From concept ideas to product launch, our collaborative approach ensures that the final result exceeds your expectations. Discover how our expertise in system development can help you achieve your goals.
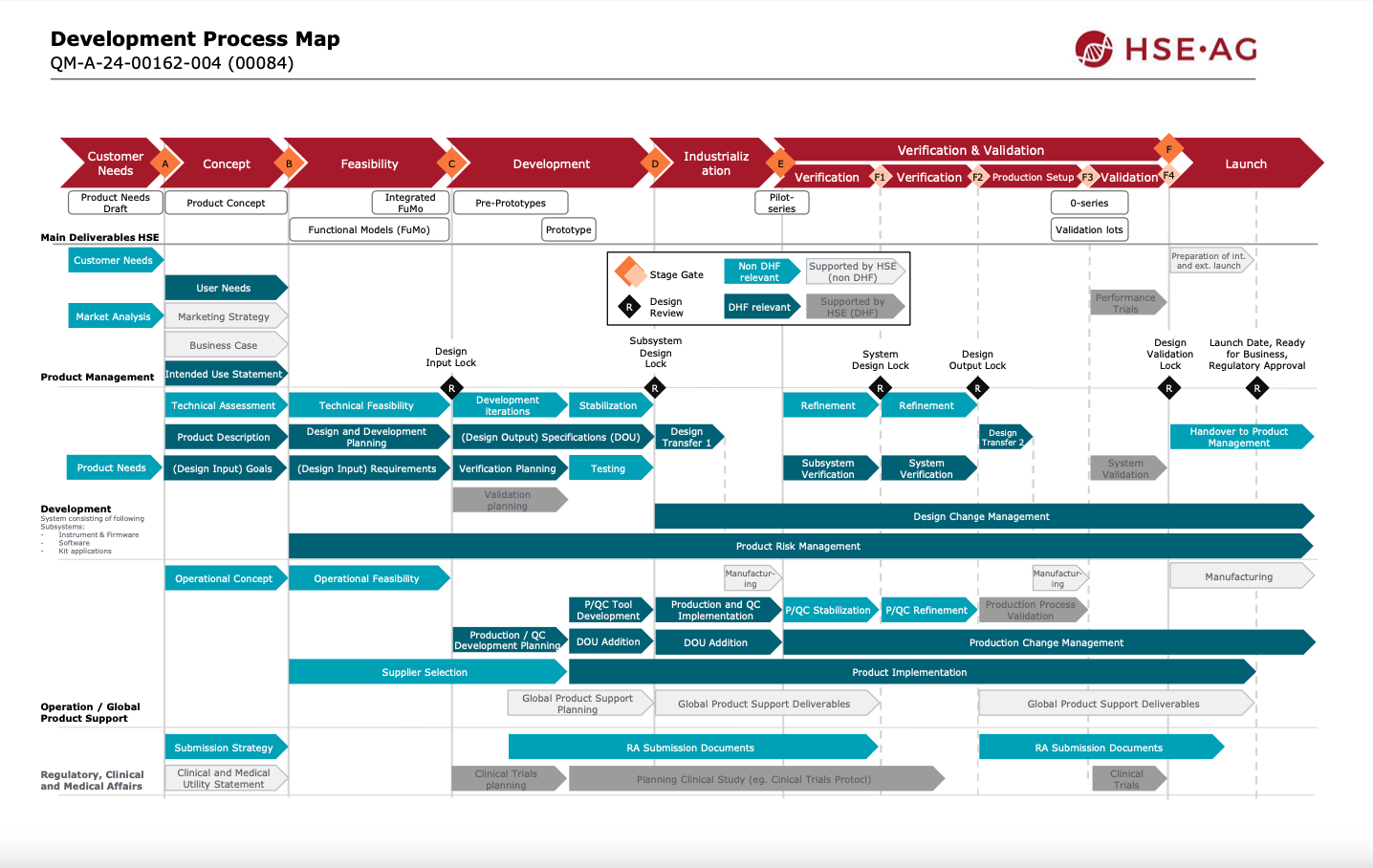
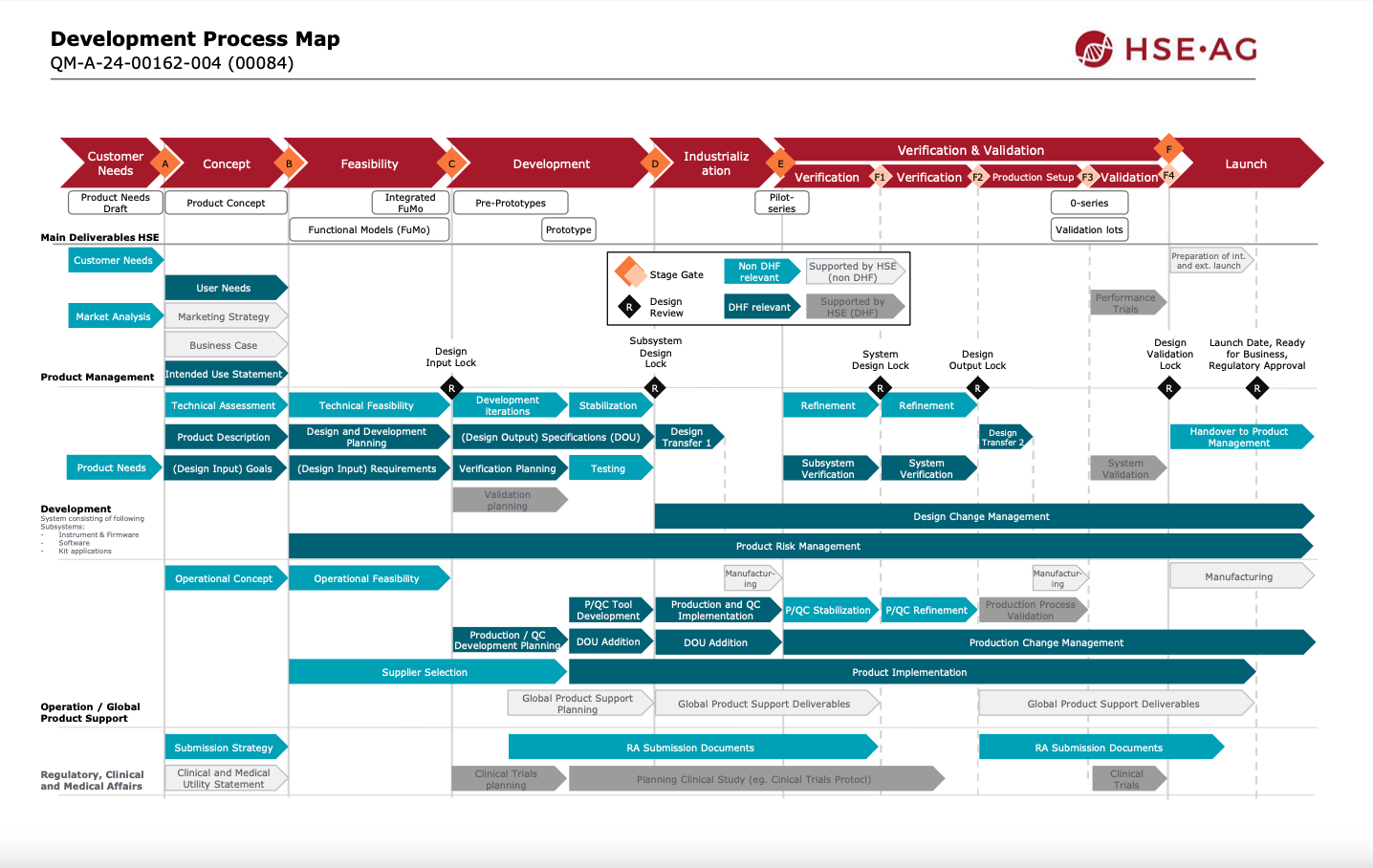
Efficient product development
Our systematic system development process (EN ISO 13485 certified) takes your ideas from concept to series production, with the goal of delivering system solutions that meet the specific needs of your application. Our team of experts works closely with you every step of the way, from the initial consultation to product launch and beyond, to ensure that our solutions align with your goals and vision.
Our system development process
Product vision
The product vision phase of a development process is a crucial step in determining the direction and success of a product. It sets the base for the entire development activities by defining the product's goals, target user, and overall market positioning. This phase helps to align the HSE development team with the customer, including relevant stakeholder, internal development team, investors, and customers, on the desired outcome of the product. A clear and concise product vision sets the tone for the entire development process and ensures that all efforts are focused on delivering a product that meets the needs and expectations of its intended users.
Concept
HSE supports the customer development team to bring the vision to a concept. This phase defines the overall project setup, the requirement and risk management, and the stage gates including defined deliverables and of course the system concept and architecture. A joined project kick-off meeting helps to establish a common understanding of the project and customer needs. The project team aligns on the collaboration tools, development process and the needed documentation. Requirement and risk management tasks and responsibilities are defined and initial documentation drafted. The system concept and architecture describe the instrument, its functions, and technical risks including the risk assessment. At the end of the concept phase a stage gate meeting will be held, where all results of the phase and the overall updated project plan are presented to all key project members.
Feasibility
The technical feasibility phase will result in a proof of concept and technical feasibility confirmation, with main functions tested to reduce technical risks. The demonstration with functional models is foreseen to show full functionality of the proposed concept. Results from the requirement engineering are used to refine the instrument concept and revise the Design Input Requirements. With the confirmed concept, a full set of approved requirements and an updated risk documentation the initial series product cost estimation can be updated.
Development
The development phase includes design development, prototype iterations till the fully tested final version and ends with subsystem (instrument / consumable / firmware & software) design lock. Each prototype iteration will undergo relevant mechanical, fluidic, electronic (including pre-EMC), system functionality, and dedicated user testing. The prototypes will be intensively used for firmware and software development and are continuously improved and updated prior to the industrialization phase. HSE produces the prototypes under early involvement of the series manufacturer to ensure a smooth transfer to production in the next phase. Development testing may include biological runs in our own S2 labs or environmental testing and accelerated aging in our climate chamber.
Industrialization
The industrialization phase will focus on smooth, cost-effective production in any manufacturing line. This phase includes transferring all technical documentation to production, adaption of parts and modules according to sub-supplier feedback following HSE design change management process. Our team support the manufacturer with technical, production, and design know-how. Our experience ensures a smooth design transfer to our established contract manufactures or to any other (including customer) production site.
Verification and Validation
The sub-system and system verification will be executed according to the testcases which were derived from the requirements according to the verification plan. A defined number of pilot units from the series manufacturer is required to confirm the product, process, and quality control design. The instrument verification also covers the final EMC-testing, transportation testing and the safety testing which is needed for defined certifications. The verification results are reported in the verification report.
Post Launch Support
HSE often supports our customers even after the product launch. We will provide customer access to the original development team for post-launch activities. Services can be offered such as sustaining engineering, change management, field updates, obsolescence management, and support of the global product service organization.
How we guarantee project success
Alignment
- Teams, processes, and nomenclature
- Agile vs. waterfall project structure
- Setup shared database
Project
Communication Plan
- Steering committee and project leadership
- Core team and technical team
- Regular meetings
- Regular reports on scope, costs, and timeline
Design Control
- Tool-supported requirements management
- Tool-supported verification planning
- Complete traceability according to V-model
Design Transfer
- Establish design change management
- Design experts responsible for transfer to production
- Support for production process implementation
Design for Manufacturability
- Alignment on design needs for manufacturability in early project phase
- Established Design for Manufacturing (DFM) program
Change Control
- Upon change request from customer
- Upon change request from manufacturer